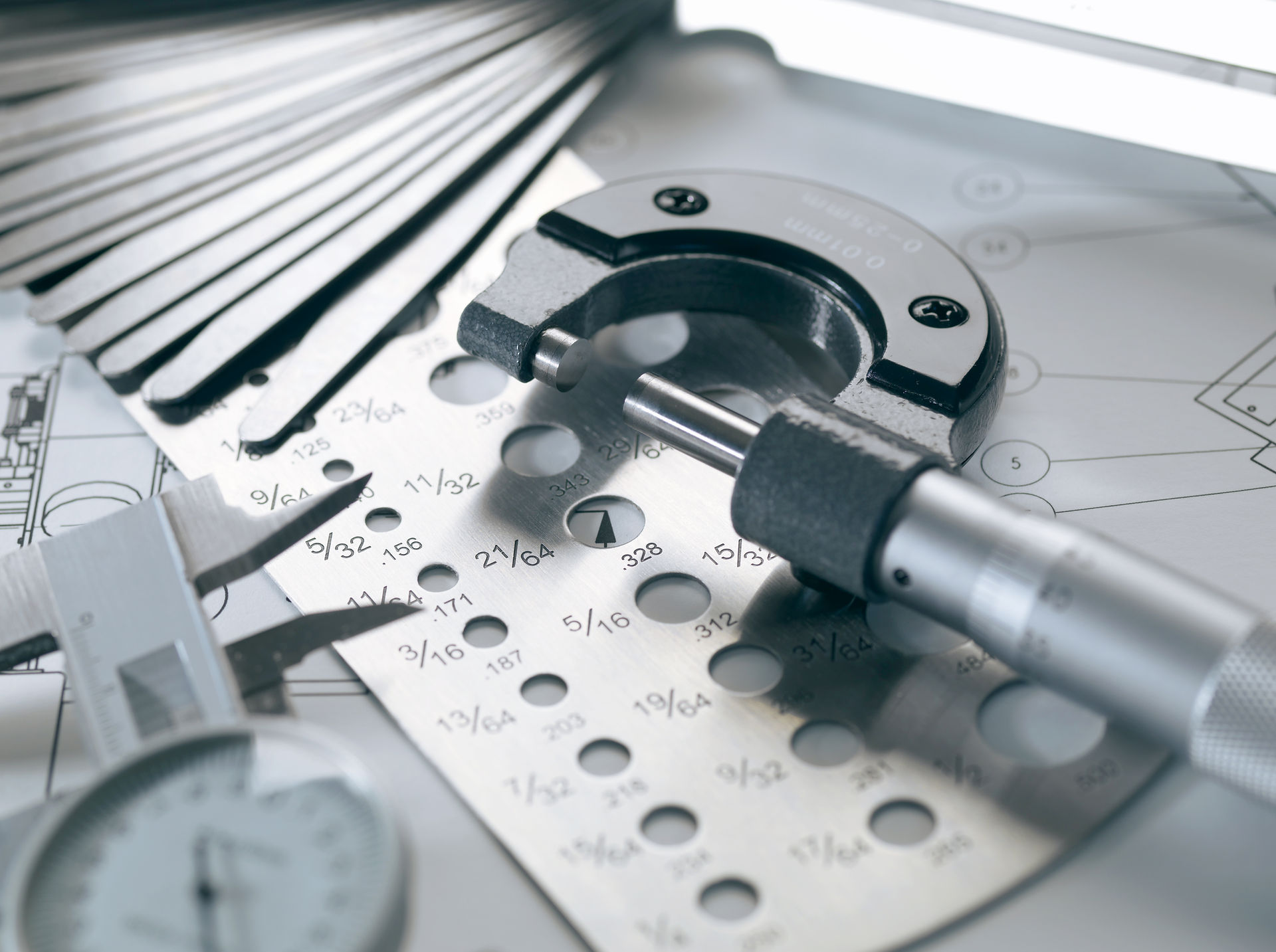
testing methods
Strength Test Methods:
A 5000-lb test vehicle will be used to determine if the jack is capable of lifting the vehicle 2-ft off the ground. A safe testing area will need to be arranged. A pulley system will support the car just in case the frame fails, and this will keep the car undamaged. If the jack were to fail and the pulley support system wasn’t present it could potentially cause damage to the user and the test vehicle. If this test cannot be performed and the resources cannot be acquired then a compressive test could be performed on the jack to determine if the hydraulic cylinder and frame can support a 5000-lb loading at different lift angles. This compressive test is a lot safer than using a test vehicle but it won’t produce the same results. A testing garage has been pre-arranged to complete the initial strength and performance test.
​
Stability Test:
This test is designed to determine how much the Auto-jack displaces from the top frame to lower frame when a side load is applied to the jack. This test will be conducted using the hanging scale acquired from the machine shop and anchoring it to the top of the jack frame. A variety of loads will be applied by pulling the scale horizontally; the displacement can then be measured using a square from the top frame. The jack frame should not displace more than 1 inch regardless of what the side load is (under 100-lbs set requirement).
Hydraulic Pressure Test:
An initial pressure test will be performed on the hydraulic cylinder before it is mounted into the jack to ensure that cylinder will be able to withstand the pressure needed to efficiently support/lift the 5000-lb loading. Refer to Hydraulic/Pneumatic part of this project for further hydraulic/pneumatic cylinder and pump testing methods.
Overall Frame Weight Test:
A scale accurate to the tenth of a pound will be used to test the overall weight of the jack frame, since the frame will already be assembled the weighing process will be simple. This weight test will determine if the initial design requirement was met and if the jack proves efficient.
Overall Closed Height Test:
This test will simply be completed by collapsing the frame entirely until the hydraulic cylinder is completely extended and measuring the vertical closed height of the jack frame using a tape measure. This measurement will determine if the initial design requirement was met and if the jack proves efficient.
Test #1 (lift height vs. time)
Test #1 Description (Lift Height vs. Time):
​
Test number one was a dry lift test (without a vehicle), to determine if the jack was capable of meeting the 2-in/s of lift design requirement, in addition to achieving a total lift height of greater than 2 feet. The resources that were used to complete this test was a stop watch and a tape measure, the completed data sheet can be found in Appendix I-2 of the engineering report. The first test proved the Auto-Jack’s success, once all link arms and sleeves were greased/lubricated seven test trials were performed. Throughout the seven test trials the max lift height was reached during each trial, the max lift height was measured to be 32.25-in, which is well over the 2-ft (24-in) design requirement, this is total height increase of over 34%. This height will allow the user to perform maintenance underneath the vehicle with ease. The other portion of this test focused on the time it took for the jack to reach the full lift height of 32.25-in, and the average lift per second of time. A stopwatch was used to record the total elapsed time until the jack was fully lifted, the first trial yielded a time of 7.37-sec. After the seven trials were completed an average lift time of 7.33 seconds was calculated. Since the jack is being lifted with hydraulics and the fluid pressure is constant inside the cylinder the total time can be divided by the max lift height to determine the time it takes the cylinder to lift the jack 1-inch, this time was calculated to be 4.40-in/sec, this is well above the design requirement initially set for the jack.

Test #2 (VEHICLE LIFT TEST)
Test #2 Description (Vehicle Lift Test):
​
The second test was the physical vehicle lift test, basically proving if the Auto-Jack is capable of lifting the test vehicle. The test vehicle being used to complete the lift test was a 2001 Ford Ranger Edge 4x4, which is the heaviest ranger Ford manufactures. Initially the tests were going to be conducted using a 2001 Honda CRV, unfortunately when mounting the gauge to the cylinder the jack wouldn’t fully close, which ultimately meant the jack wouldn’t fit underneath the CRV’s rear differential. The first trial was conducted and deemed successful the Auto-Jack was capable of lifting the rear end of the truck with ease, Approx. 1336-lbs. The force on the jack was found using the equation in Appendix G, this appendix also includes the datasheet for final completed test. After completing the test and analyzing the data it was clear to see that the pressure is linearly proportional to the weight on the jack, as the pressure in the system increases the force on the jack increases, which is what was concluded before the test was initiated. In conclusion the hypothesis generated and the success of the jack were both satisfied after completing this test. The next test will involve lifting the entire vehicle approx. 4500-lbs, theoretically since the jack is only operating at 1/3 of its capable system pressure, lifting the entire vehicle should be no issue.

additional testing photos

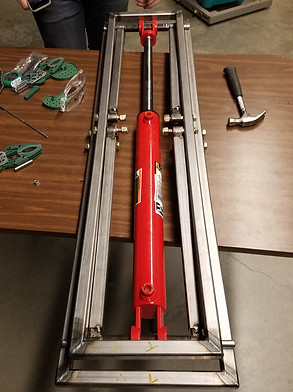

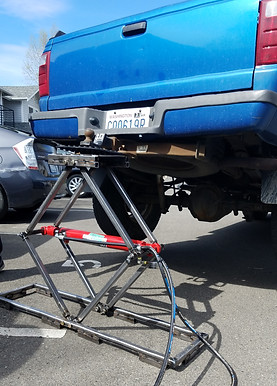